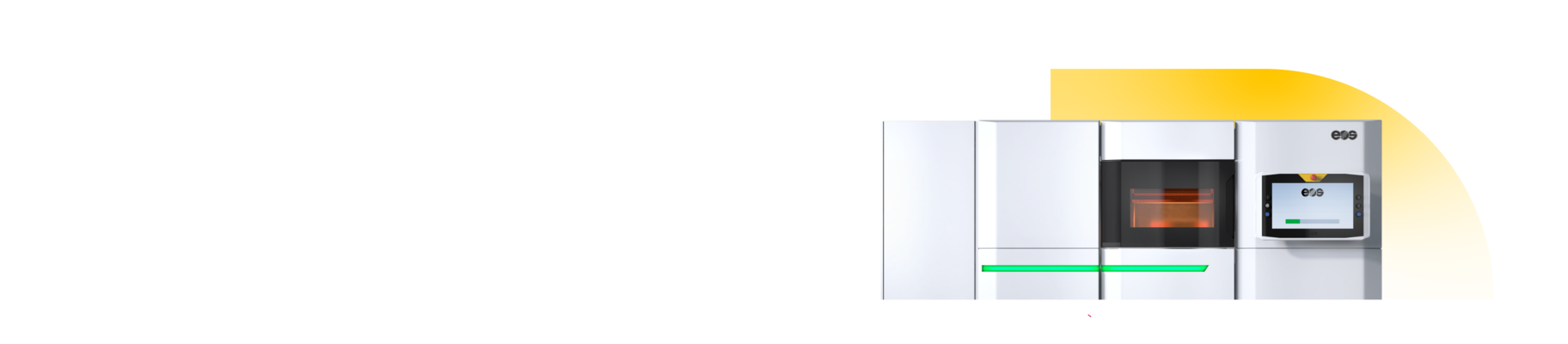
EOS Polymer 3D Printers
Fast, Reliable and Highly Efficient
Compare Our Polymer 3D Printing Solutions
While industrial 3D printing promises more flexibility and creative freedom than traditional manufacturing, understanding different materials and technologies can be a challenge. Here’s your easy path into the limitless world of polymer 3D printing.
Selective laser sintering (SLS), the technology perfected by EOS, uses plastic polymers in powder form that are fused using a precise laser. The result is robust functional parts with high design freedom, as no support structures are required.
The innovative Fine Detail Resolution (FDR) technology uses a laser beam that takes precision to new heights. This is opening the door to extremely stable, filigree parts with an ultra-smooth surface finish across different materials and applications.
Number & Laser Type |
Build Volume (mm) |
Machine Dimensions (mm) |
Weight (kg) |
FORMIGA P 110 Series
With a small footprint and build volume, the FORMIGA P 110 Series stands out as a compact and efficient solution for industrial polymer 3D printing. It not only offers excellent part quality but also consumes minimal floor space. This makes it an ideal choice for businesses seeking space-efficient 3D printing technology to achieve repeatable results across machines.
The FORMIGA P 110 FDR’s fine laser beam takes precision to new heights, opening the door to extremely stable, filigree parts with an ultra-smooth surface finish across different materials and applications.

EOS P3 NEXT
The EOS P3 NEXT is a mid-sized 3D printer for a wide range of industrial applications, promising incredibly homogeneous mechanical properties throughout the entire build volume.
This highly productive and reliable system can easily be integrated into IIoT environments through EOSCONNECT Core. That way, you’ll enjoy a fully digital 3D printing process from the CAD model all the way to functional parts. With 14 plastic material choices and 26 parameter sets, it can effortlessly adjust to the most diverse industry requirements.

EOS P 396
The EOS P 396 is a mid-sized 3D printer for a wide range of industrial applications, promising incredibly homogeneous mechanical properties throughout the entire build volume.
This highly productive and reliable system can easily be integrated into IIoT environments through EOSCONNECT Core. That way, you’ll enjoy a fully digital 3D printing process from the CAD model all the way to functional parts. With 14 plastic material choices and 26 parameter sets, it can effortlessly adjust to the most diverse industry requirements.

INTEGRA P 450
This additive manufacturing system empowers designers, production engineers and material makers alike with an impressive array of new user-friendly features. Its unprecedented material processing at up to 300° C allows for 3D printing application scenarios using polymer materials that previously weren’t available for certain designs.
Thanks to the integration of 8-zone quartz heating and a thermal imaging camera in the build platform, you can benefit from consistent quality control and data capture across your production line. The modular, future-proof design, combined with EOSPRINT 2, extends the 3D printer’s lifecycle and sets you up for using high-performance polymers in an industry 4.0 setting.
This system is available only to customers in North America.

EOS P 500
With the lowest costs per part and automation-friendly software and hardware, the EOS P 500 offers the latest generation of industrial 3D printing. A system availability of 92% and homogeneous part properties for every build allow you to reliably process plastic on an industrial scale.
Accessories for optimized part and material flow, as well as automated interfaces, increase operating time by at least 25% compared to conventional 3D systems on the market.

EOS P 770
As the SLS printer with the largest build area on the market (150 liters), the EOS P 770 is perfectly suited for additive manufacturing of large parts with high throughput. Benefit from reduced build time and cost per part due to optimized temperature management, enhanced layering speed, and powerful lasers.
The energy input is effectively homogenized by the EOSAME feature, resulting in consistent mechanical properties and dimensional accuracy across the entire build volume. Notably, the lasers’ overlapping zones make for a seamless production without any discernible edges.
