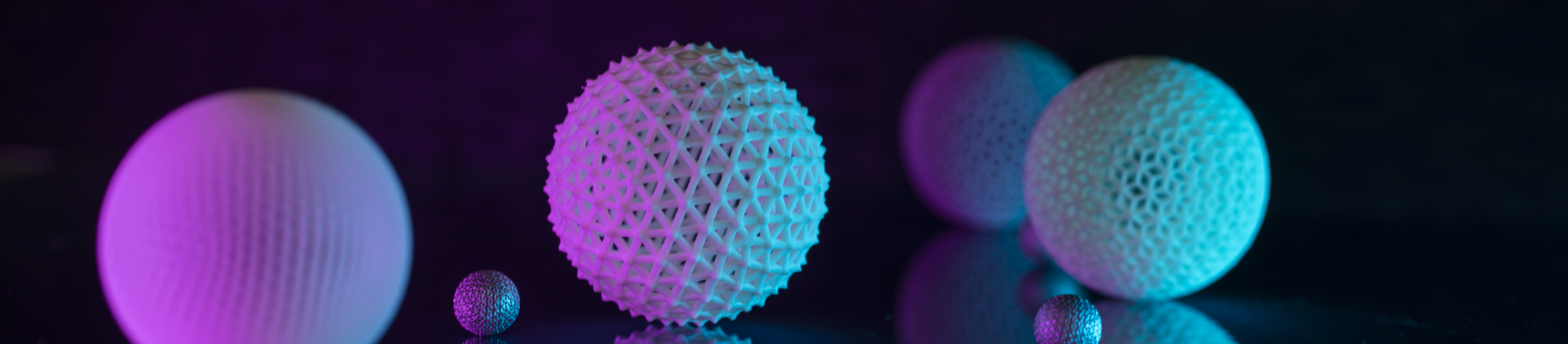
3D Printing of Consumer Goods
More Diversity in Design and Engineering
Make Any Shape Into a Product With Additive Manufacturing
3D printing, or additive manufacturing, opens up a whole universe of new possibilities: Users can make any conceivable shape into a real product cost-efficiently, flexibly and quickly with minimal consumption of materials. Additive manufacturing builds objects up layer by layer in a single step. This targeted application of material makes it possible to manufacture products that are both stable and very lightweight.
AM is based on a digital process. This guarantees consistently high quality, ideal scalability and short lead times. Product designers can count on the manufacturing process to make furniture such as lamps or chairs, but also fashion items such as jewelry, handbags or glasses with complex shapes and structures.
Any conceivable form is possible, and new business ideas can be quickly realized. 3D printing enables local on-demand production: You can manufacture your parts exactly where you need them. You can configure a pair of shoes or a watch online, then print them on site.
Sports, Lifestyle and Consumer Goods
3D Printing Optimizes Design, Functionality and Customization