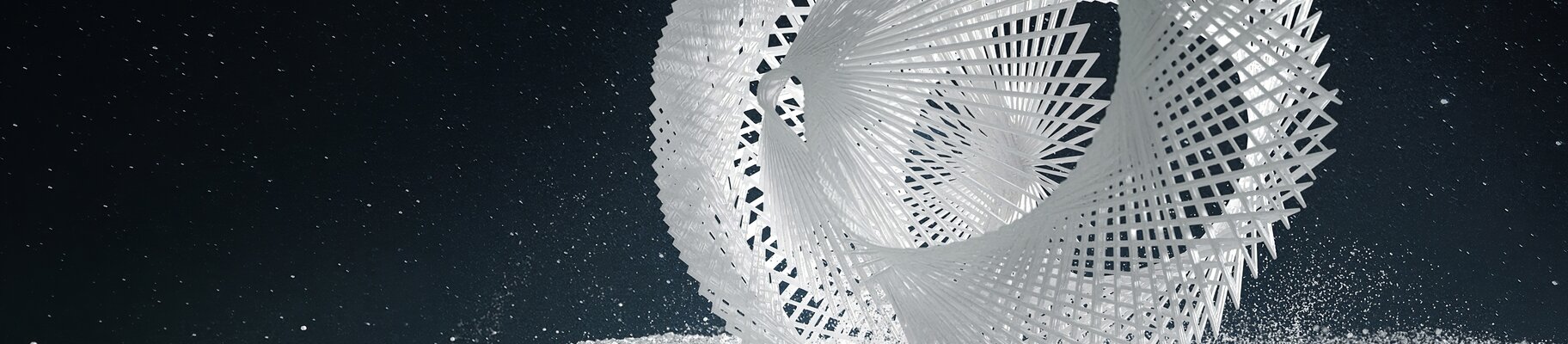
Selective Laser Sintering (SLS)
How Does it Work?
Selective Laser Sintering (SLS) is an advanced additive manufacturing (AM) technology that revolutionized the way prototypes and end-use parts are produced. Developed in the late 1980s, SLS is a powder bed fusion 3D printing process that uses a high-powered laser to selectively fuse powdered materials, typically polymers or metals, layer by layer, to create three-dimensional objects.
The fundamental principle behind SLS involves the use of a powder bed as the build material. This powder can be composed of various materials, such as nylon, TPEs and TPUs, depending on the desired end product. The process begins with a thin layer of powder being evenly spread across the build platform. The laser then scans and selectively sinters the powder, melting it together to form the first layer of the object being fabricated.

What are Key Advantages of SLS?
One of the key advantages of our SLS polymer 3D printers is their ability to produce complex and intricate geometries with a high degree of precision and high quality surface finish. This makes SLS a go-to choice for a variety of industries, from aerospace and automotive to healthcare and consumer goods.
SLS offers inherent advantages over other additive manufacturing methods. The lack of support structures, as seen in stereolithography or fused deposition modeling, means that complex geometries can be built without the need for additional support removal steps. The unused powder in each layer also serves as a natural support during the printing process, reducing the risk of warping or distortion. Our SLS technology has emerged as a powerful and versatile option to produce complex, functional parts with a variety of materials.