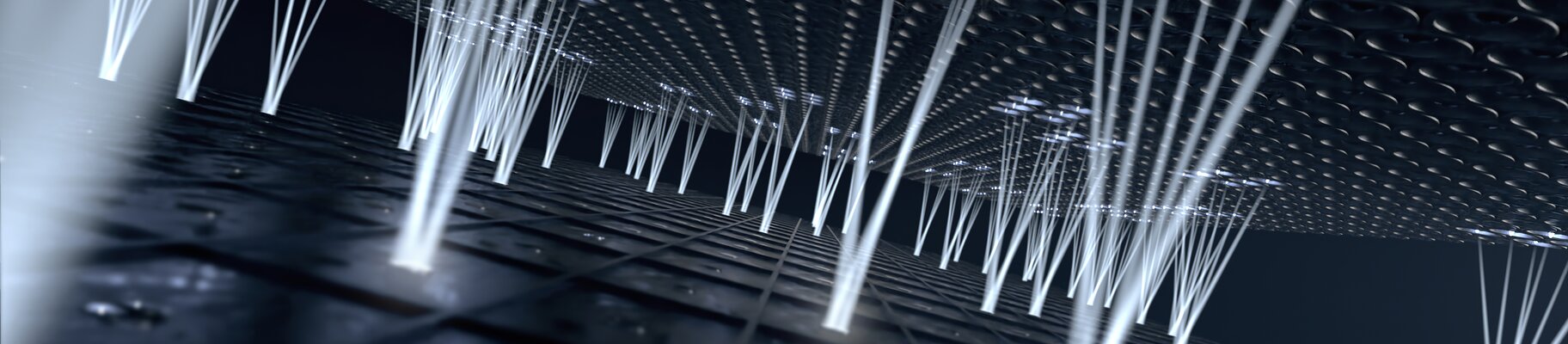
Laser Pro Fusion
A Million Diode Lasers for Production up to 10 Times Quicker
The Technology for Tool-Free Injection Molding
With LaserProFusion technology, EOS presents a revolutionary process for additive manufacturing with plastics. The material is melted by almost a million diode lasers to create the desired part, and the build process is so productive that it can even replace injection molding in many applications.
The new LaserProFusion technology is an innovation developed for maximum productivity. As pioneers with more than 30 years of experience in additive manufacturing, EOS is constantly optimizing the interactions between the powder material and the laser. The new technology significantly reduces the duration of the exposure time, which is independent of the number of parts and their geometries.
"With LaserProFusion technology, we are achieving a new level of productivity in series production using industrial 3D printing with polymers. In many applications, the technology can provide a tool-free alternative to injection molding. This will make industrial 3D printing attractive to a completely new market in the future."
Virginia Palacios | Chief Business Officer Polymer Solutions | EOS GmbH
Unlike previous laser sintering methods, the method doesn’t use one CO2 laser that travels across the build space. Instead, up to a million diode lasers are used simultaneously. Together, these lasers achieve a maximum total output of up to 5 kilowatts. At each layer, the lasers are only activated to melt the powder at the pixels specified in the CAD data of the part.
LaserProFusion is tailored to the requirements of series production, accelerating product development, and enabling tool-free injection molding. In many applications, it can even serve as a replacement for injection molding. EOS LaserProFusion can achieve cost savings of up to 20 %.