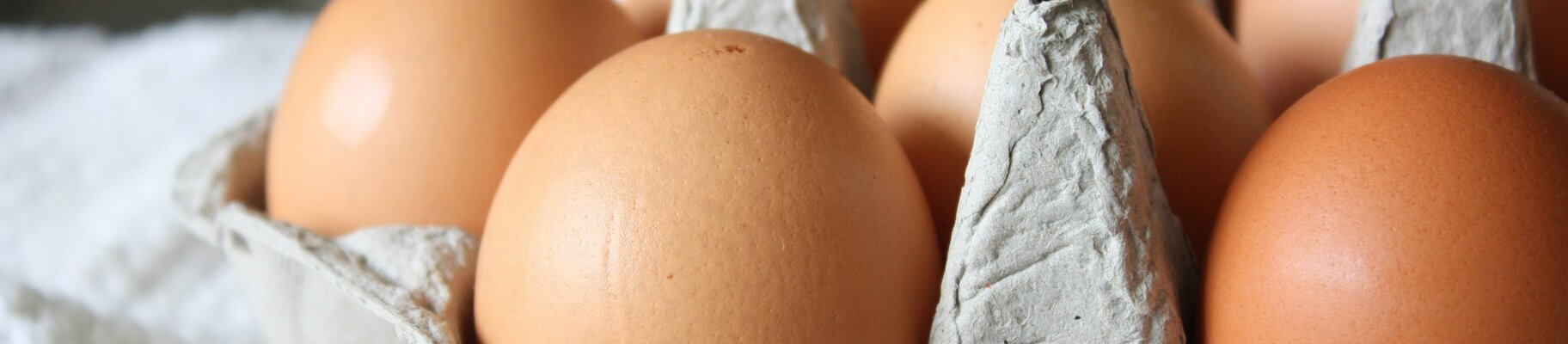
3D Printed Tools for Molded Fiber Production
Payr Engineering | Case Study
Cleanly Packaged
- 50% lower tool cost
- Production time decreases to a few weeks
- Profitable even for small batch sizes
Handle something like a raw egg - a familiar expression. As tough as an egg shell is, the well-known egg carton is usually the first choice for safe transport home. The molded pulp packaging offers protection and is environmentally friendly. The Austrian engineering service provider Payr has optimized the tool for its production by means of additive manufacturing, helping to produce it faster and more cost-effectively. In addition, the transport distances could be shortened and smaller quantities are possible.

"Using EOS machines we are able to produce robust components that couldn’t be manufactured with machines from other suppliers."
Peter Paul Payr | Managing Director at Payr Engineering
Challenge
Molded pulp - the word itself is not as common as the material. Whether made from waste paper or renewable fibrous materials such as grasses, more and more companies are using recycled and recyclable materials as protective packaging. In the retail environment, these range from the egg carton mentioned at the beginning to bespoke packaging that protects electronic or household appliances. Thanks to technological advances, the material can do even more today. Fat-repellent, water-resistant - all this is possible without plastic.
As a result, the material has also become interesting for other fields of application. Up to now, the problem has been the number of pieces needed for the packaging. One of the reasons for this is the production process. Basically, the material dissolved in water—the so-called pulp—is sucked into a perforated mold that has a coating of many small openings by means of a vacuum. The liquid drains off or is sucked off via these screens. The perforated molds were usually covered with the sieve by hand, mainly at Asian production sites - a very expensive and time-consuming procedure.
Payr addressed these issues, focusing on the tool and in particular the sieve: "Finishing such a component by hand would be too expensive in this country and is associated with long transport routes abroad, which in turn entail costs. Due to the production and manufacturing time of the traditional process, there was a potential for optimization either way," explains Peter Paul Payr, Managing Director at Payr Engineering and shareholder of the Payr Group. "That's why we looked for an alternative for the production of the screen, and found it in additive manufacturing."
Cost-effective & Sustainable
Production Process of Molded Pulp Packaging

Solution
Payr came up with a particularly innovative approach: the mold and screen used to consist of two components: a metal core and a lattice structure, which was manually shaped and applied. Thanks to additive manufacturing, an innovative drainage structure was developed that now combines the original functions of the statically stable mold and the regularly distributed drainage over the entire mold in one part. As a result, this requires only a single production step. This further simplifies production and also accelerates the process as a whole, while maintaining the same high quality.
The material chosen by Payr is the plastic PA 12, which is common in additive manufacturing. It is inexpensive and tough enough because the 3D printer used reproduces the fine screen structure excellently. Peter Paul Payr confirms that this is not a no-brainer: "EOS has an extremely high-performance product in its portfolio with the EOS P 396. The performance significantly exceeds that of other known manufacturers, especially with regard to lattice structures. We have not been able to achieve the stability of the component needed for this application with any other device."
Precision is crucial, and therefore critical to success, in order to be able to control the flow resistance of the pulp correctly: on the one hand, the geometry of the drainage structure determines how much material sticks to the mold and how stable the packaging becomes later. On the other hand, it influences how much moisture remains, which affects the drying time. Of course, additive manufacturing also brings its "classic" advantages here, such as the great freedom of design for the mold and the short overall time required for its production.
Results
However, the moment of truth always comes when checking whether the goals have been achieved. This is where the new tool from Payr is completely convincing: whereas the procurement time used to be several months, the new combined suction unit is now available in a few weeks. Just as important - and impressive - is the cost reduction achieved through the conversion: "We can offer our customers a significant advantage here. The cost of manufacturing the tool is at least 50 percent lower than the traditional manufacturing method. And this makes 3D-printed molds attractive for packaging in small quantities or in variants," says Peter Paul Payr proudly. Due to the freedom of design offered by additive manufacturing, it is also possible to produce final packaging with different wall thicknesses, i.e. material is used only where it is necessary.
Together with the optimized screen technology, Payr reviewed the entire production process - and, on the basis of the optimized tool, was able to exploit even more potentials with its self-developed FIBRA MINI molded pulp plant. For example, the suction and drainage technology could be improved. This results in a lower energy requirement for drying and lower material costs, because the walls could be made even thinner, despite an increase in quality. Less material at the same time means benefits throughout the entire life cycle, from printing to recycling.
There is no way to quantify yet another benefit for businesses: the supply chain becomes much more resilient. A more cost-effective relocation of a production step is not only a rarity, but also increases the independence form set routes for suppliers of molded pulp products. At the same time, this streamlining of the supply chain offers further environmental benefits - because if something does not have to be transported halfway around the world, it naturally has a smaller CO 2e footprint. Even more important for sustainability, however, is the fact that molded pulp becomes even more competitive and can thus replace more and more plastic packaging.
For Payr Engineering and its customers, the conversion in the production of the production tool for molded pulp is therefore a successful project in many ways. "Where else can transport routes be shortened, production restored and at the same time costs reduced and quality increased," asks Peter Paul Payr. And this whole chain of benefits begins with technology: additive manufacturing. In future, more and more products such as raw eggs will find their way from the producer to the customer.
Precise & Stable
3D printed pulp mold with innovative lattice-shaped drainage structure made of PA 2200 plastic material


"We can eliminate quality fluctuations while reducing costs and time to market. Our customers become more resilient in the supply chain, reduce transportation costs and the quantity of plastic packaging."
Peter Paul Payr | Managing Director at Payr Engineering
EOS Case Studies
Explore three decades of pioneering 3D printing excellence with EOS