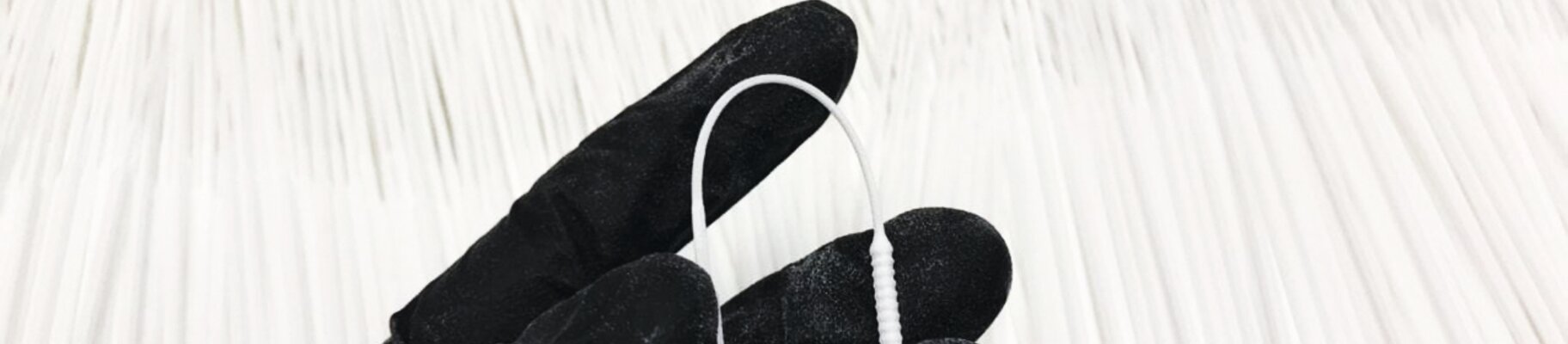
Collaboration for Mass Production of Certified 3D-Printed Nasal Swabs
AENIUM & Burloak | Success Story
Production of Medical Devices with Industrial 3D Printing in Europe and North America
The COVID-19 pandemic tested global health care capabilities. Supply chains were disrupted, requiring local agile solutions for certified medical devices. Many companies are collaborating with their local governments to provide critical medical devices such as ventilator components, ICU critical parts, face shields, face mask filters, etc., to fight the shortages.
In this context, a collaborative R&D consortium was created in March 2020 to develop certified medical devices and ramp up mass production in North America and Europe. This consortium included Aenium Engineering and Burloak Technologies, who worked closely with EOS’ Additive Minds applied engineering team, the Canadian and Spanish health authorities and hospitals, as well as a Spanish genomic laboratory (ITALCyL).
"This is the first 3D-printed nasal swab certified by a government agency and was made possible by collaboration between Aenium, Burloak, Additive Minds and many others. It demonstrated the great opportunity for empowering private-public consortia in the fight against global challenges using industrial 3D printing – an inspiration for others worldwide."
Jose Miguel Ampudia | Chief Technical Officer and R&D Manager | Aenium Engineering
Challenge
The demand for COVID-19 test kits combined with the empty inventory of conventionally manufactured nasal swabs made it clear that additive manufacturing would be the ideal technology for bridging this gap. However, there were challenges that needed to be overcome.
The first challenge was the sampling itself. It is essential for the test swab to preserve the virus’s integrity to allow RNA detection by means of reverse transcriptase real-time PCR. A solution is needed with a porous-specific activated surface on the head plus a highly flexible stick which cannot be manufactured conventionally.
The second challenge was the high demand for a cost-effective solution. Aenium and Burloak developed a model for producing up to 40 000 swabs per day on multiple EOS additive manufacturing systems.
And the third challenge: Nasal swabs are a class IIa medical device, requiring a specific certification for testing and qualification to fulfill medical standards. Therefore, a typically long certification procedure with the pub



Result
Aenium is working with the Spanish government and hospitals to produce hundreds of thousands of medical nasal swabs for use in COVID-19 test kits. ITACyL, a public laboratory, and other Spanish laboratories have tested the performance and done the clinical validation to successfully achieve AEMPS (Spanish Agency of Medicines and Medical Products) certification for the mass production of this IIa class medical device.
Burloak is helping North American hospitals and public health systems to increase production capabilities and fight against stockouts of this critical medical device.

- Clinical tests have demonstrated the performance of the 3D-printed nasal swab, a class IIa medical device, as an effective option compared to the commercial nasal swabs.
- EOS industrial 3D printing polymer solutions enabled agile production for a fast response due to supply chain gaps with a highly accepted material in the medical sector.
- Nasal swabs can be produced anywhere in the world according to a decentralized model thanks to additive manufacturing.
- On-demand manufacturing: No expensive tooling needed, just start the systems and qualify the process.