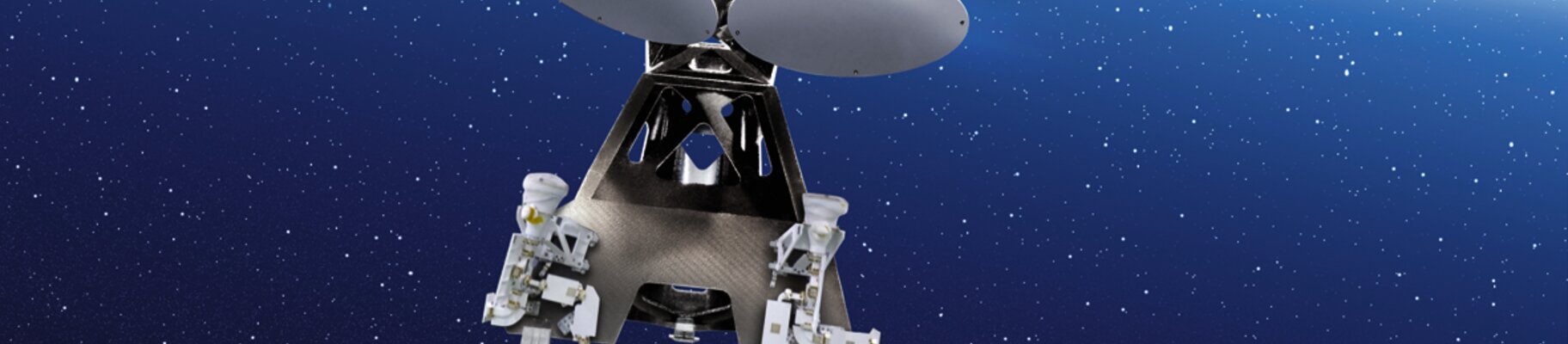
Airbus Defence and Space Advanced Manufacturing Process by EOS Optimizes Satellite Technology
Airbus Defence and Space Uses EOS Technology for the Production of Satellite Parts | Success Story
-
Improved temperature resistance
-
Reduction of production time
-
Reduction of production costs by more than 20%
"The Additive Manufacturing method brought measurable benefits to critical aspects of the project, without requiring cuts to be made elsewhere. No compromises - this is something engineers like to hear, but don’t get to hear very often."
Otilia Castro Matias | COC Antennae | Airbus Defence and Space
The current generation of satellites includes specific brackets that serve as a link between the body of the satellite and the reflectors and feeder facilities mounted at its upper end. The engineers at Airbus Defence and Space faced two key challenges with regards to the construction of these retaining brackets: on the one hand, the brackets must fix the securely to the body. On the other hand, however, the task of the brackets is to mitigate the extreme temperature fluctuations in space.
The choice fell to the Additive Manufacturing technology for metal parts offered by EOS. This meant that titanium was still usable as a tried and tested material. It also allowed the design of the components to be adapted easily.
The new devices meet all expectations of the experts involved. Most important of all is the improved temperature resistance of the entire structure, which now can easily and permanently withstand a margin of 330 °C under a force of 20 kN. In addition to the technical advantages, targeted cost reductions were achieved: savings in production alone amount to more than 20 %. What is more, the engineers successfully put the part on a diet: the weight advantage is about 300 g, which means nearly one kilo per satellite.

"The use of titanium as the material for the retaining brackets of our satellites has proven highly effective. The main weakness, however, was the connection of the brackets with the carbon panel of feed and reflector assembly because here the thermal stress was a negative factor. Thanks to Additive Manufacturing, we were able to redesign the bracket and eliminate this vulnerability. There were other benefits, too, such as shorter, more cost-effective and more lightweight production."
Otilia Castro Matias | COC Antennae | Airbus Defence and Space
The Results at a Glance
- -20% Reduction of production costs
- -300 Grams Reduction of weight