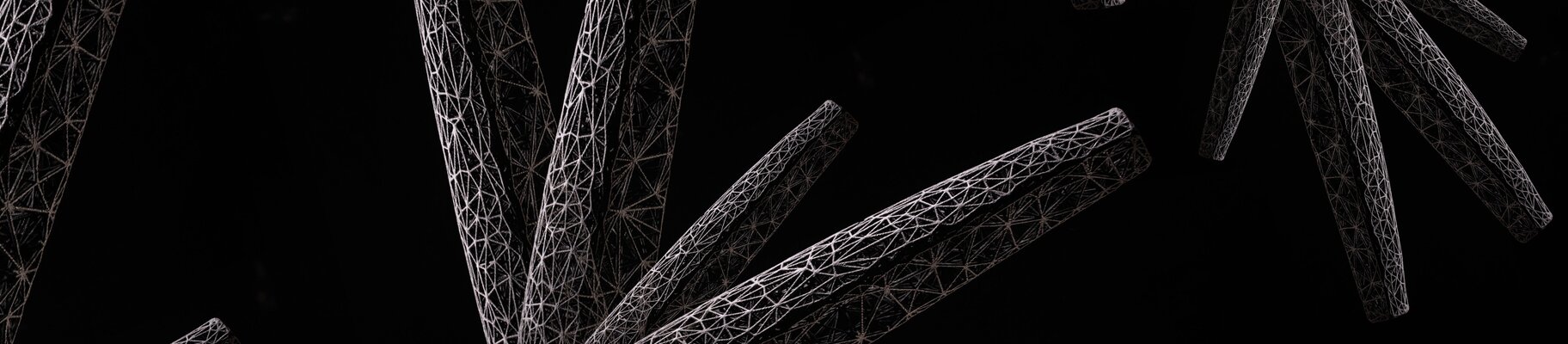
formnext 2019: EOS First Supplier to Develop CO Laser Solution for Industrial 3D Printing
Polymer-based FDR technology for superfine surfaces and extremely delicate components will pave the way for new series production applications.
____ Krailling, Germany, November 19, 2019
EOS, the world's leading technology supplier in the field of industrial 3D printing of metals and polymers, is showcasing its Fine Detail Resolution (FDR) technology for processing polymers for the first time at the formnext trade show in Frankfurt (November 19–22, 2019, hall 11.1, stand D31). EOS is therefore the first manufacturer to develop a solution for powder-based industrial 3D printing using a CO laser. This will make it possible to produce extremely delicate yet robust parts with fine detail resolution surfaces and minimum wall thicknesses of only 0.22 mm. It will open up new applications for series production and will offer an even broader variety to the industry when it comes to choosing the right 3D printing technology from EOS for processing polymers.
FDR technology for surfaces with fine detail resolution
FDR is a highly suitable solution wherever delicate structures, surfaces with a fine detail resolution and thin wall thicknesses are the foremost requirements. Unlike the existing EOS product range, a 50-watt CO laser is being used for this. This laser type creates an ultra-fine laser beam with a focus diameter that is only half the size of current SLS technologies. This enables completely new exposure parameters resulting in parts that have superfine surfaces. Initially, the certified material PA 1101 is used. It is processed in layer thicknesses of 40 and 60 µm and features both high impact resistance and elongation at break. Moreover, it is made from renewable raw materials.
The FDR technology is being developed for the EOS polymer production platform and opens up options for completely new applications in the field of polymer-based additive manufacturing, such as for filter units and fluid channels, plugs, and other electronic components as well as consumer goods such as eyeglasses. EOS is presenting this technological concept for the first time at the formnext 2019 with the aim of obtaining some early market and customer feedback.

The new technology will combine the best of two worlds – the detailed resolution of stereo lithography (SLA) with the durability and quality of selective laser sintering (SLS)."
Dr. Tim Rüttermann, Senior Vice President Polymer Division
He continues: “In future, depending on application requirements, customers will therefore be able to choose between the existing EOS P 500 version with a CO2 laser for high productivity and material flexibility; or the CO laser-based FDR technology for manufacturing extremely delicate components; or, if the focus is on maximum productivity with dedicated application material, they can decide for the upcoming EOS LaserProFusion technology concept that was showcased for the first time at the formnext 2018."
EOS P 500 SLS technology: high productivity and material flexibility
The EOS P 500 platform is primarily designed for companies that want to produce high-quality polymer components reproducibly on an industrial scale using additive manufacturing. In an initial step, a CO2 laser with a focus diameter of 0.5 mm and a laser output of 2x 70 watts will be used on the platform. This highly efficient, automatable system makes it possible to minimize costs per part and process polymer material classes such as PA 12, PA 11, PA 6, TPU, and other high-performance polymers. The use of this platform will also open up applications in the mobility and automotive industry as well as in the manufacturing of electronic components.

EOS LaserProFusion: for highly productive injection molding tool-free
Compared with the FDR technology, EOS LaserProFusion technology is designed for maximum productivity with a constant focus on high-quality results. In contrast to the above-mentioned solutions, up to 1 million diode lasers with a maximum accumulated laser power of over 5 kilowatts are used here. The exposure speed is independent of the component geometry. This technology is geared to the requirements of series production, shortens product development times, enables tool-free injection molding, and can even be used as a replacement for injection molding in many applications. EOS LaserProFusion can therefore cut costs by up to 20 percent.
At the same time, the technology takes account of ever-shorter product cycles and an increasing demand for individualization, thus opening up completely new fields of application. EOS LaserProFusion is also planned to build on the EOS P 500 platform.

About the Company
EOS
EOS is the world's leading technology supplier in the field of industrial 3D printing of metals and polymers. Formed in 1989, the independent company is pioneer and innovator for comprehensive solutions in additive manufacturing. Its product portfolio of EOS systems, materials, and process parameters gives customers crucial competitive advantages in terms of product quality and the long-term economic sustainability of their manufacturing processes. Furthermore customers benefit from deep technical expertise in global service, applications engineering and consultancy.
Downloads
formnext 2019: EOS First Supplier to Develop CO Laser Solution for Industrial 3D Printing
Source: EOS GmbH
-
Polymer-based FDR technology enables manufacturing of superfine surfaces and extremely delicate components
JPG 688,10 kB -
FDR is a highly suitable solution wherever delicate structures, surfaces with a fine detail resolution and thin wall thicknesses are the foremost requirements.
JPG 2,64 MB -
Polymer-based FDR technology enables manufacturing of superfine surfaces and extremely delicate components
JPG 3,64 MB -
Valve, 3D printed with the FDR technology
JPG 4,21 MB