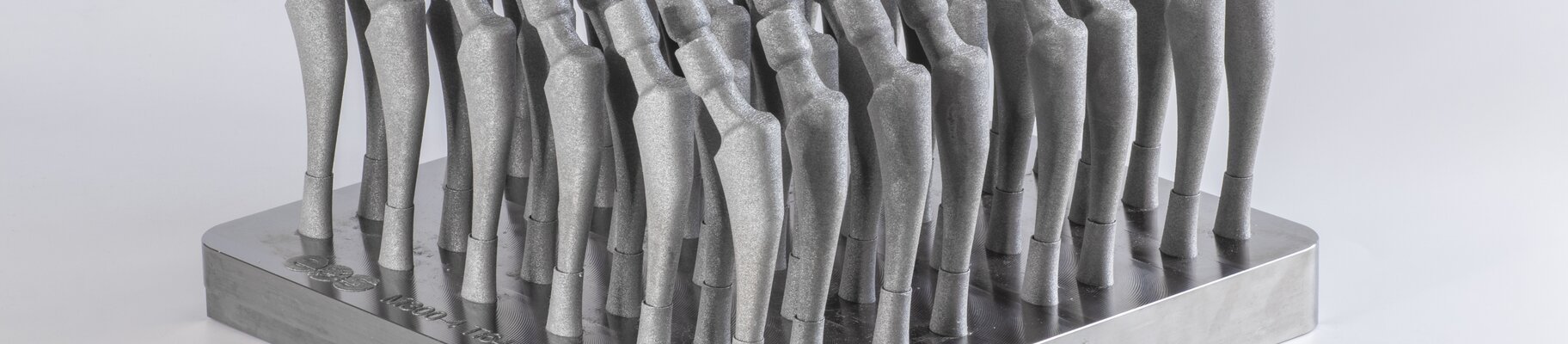
Orthopedic Implants: New Possibilities with Metal 3D Printing
October 30, 2020 | Reading time: 4 min
EOS has developed a Ti64 AM process which, combined with Hot Isostatic Pressing (HIP) heat treatment process, creates outstanding fatigue properties. The goal of this project was to highlight and test these fatigue properties on an actual implant design and to compare the results to traditionally forged Ti64 hip stems.
Opening up the possibilities of additive manufacturing
The sections below show how the knowledge, experience, and services the EOS network has to offer came together to realize this leap forward in orthopedic additive manufacturing:
Fatigue results
The fatigue tests were performed by OIC, Orthopedic Innovation Center, Winnipeg Canada. The hip stems were tested on for neck fatigue properties according to ISO 7206-6. They withstood a load of 5340 N for 10 million cycles. In this study, 2 additively manufactured hip stems were tested and both passed to a runout of 10 million cycles. This demonstrates that the fatigue properties of these AM manufactured implants were at least as good as the traditional forged Ti64 hip stem. This is the first time that such high fatigue properties have been measured on an implant manufactured with Additive Manufacturing.
Build preparation
To avoid the need of support removal and to facilitate the implant removal from the platform, the hip stems were manufactured in a “holder”. The main functionality of this holder is to provide protection against the recoater forces. (To obtain the highest mechanical properties, a HSS blade was used to ensure optimal and consistent recoating behavior.) However there is no connection between the holder and the hip stem, but rather a gap of about 0,2mm - 0,3mm, the ideal gap width was determined through a DoE. The gap size is a tradeoff between easy removability and firmly keeping the hip stems from vibrating due to recoater forces. The hip stem is held in place thanks to the friction forces between the holder, the powder, and the hip stem.
I got my inspiration for this build strategy from the Building without support post from my colleague Michael Wohlfart. It is very rewarding to bring these innovative ideas to life in a real application!
Using the Additive Works Software Amphyon
The next step was to ensure this idea would work in practice. Amphyon was used to confirm that the setup strategy did not lead to any issues, eliminating the need for a “trial and error” building strategy. A common complaint from new AM users, and even experienced AM users trying new applications, is the need to use a “trial and error” strategy for first time builds.
Simulations were run to check for recoater collision, to verify that the deformations were within tolerance, and to check for thermal stresses. This analysis provides a high quality build before building a single job, reducing cost and lead time.
This software allows pre-deformation of the hip stem to create a highly accurate part directly out of the printer, the first time. In my experience this works well, especially for small and controlled deformations which are expected for the hip stem during printing.
Achieving excellent fatigue properties
State of the art AM process
The hip stems have been manufactured using the EOS Titanium Ti64 Grade 23 process in 40µm layer thickness on an EOS M 290. The EOS M 290 was chosen for this project because it is the most qualified industrial additive manufacturing system on the market. On top of that the reliability and repeatability of the machine is exactly what is needed for great fatigue properties where a single defect can lower properties significantly. It would make sense in the future to optimize the process further for serial manufacturing, potentially improving the build rate and stability given the unique requirements of a hip stem application.
Optimized HIP Heat treatment
The excellent fatigue properties are obtained due to a combination of a state of the art AM process (mentioned above) combined with an optimized Hot Isostatic Pressure (HIP) heat treatment. Conventional HIP heat treatments are optimized to improve the mechanical properties of casted or cast-like quality and microstructure. The quality out of an EOS M 290 is much superior to this and therefore EOS has developed a HIP heat treatment which takes into account the unique microstructure of AM.
The conventional hip treatment is done at 920 °C at 100 MPa for 2 hours and is widely spread among different industries. The process developed by EOS is done at 820 °C at 140 MPa for 2 hours. This HIP cycle combined with EOS DMLS process results in fatigue strength of 795 Mpa for 10^7 cycles (N=9).
Post Processing
The post processing is rather straight forward and was performed by Precision ADM, Winnipeg, Canada. The AM process was set up in such a way that the same post processing steps as a conventional manufactured hip stem could be used. Therefore the no supports approach was chosen. The taper is machined and the neck of the hip stem was polished for optimal fatigue properties, similar to a predicate device already on the market. The results can be seen on the right.
Conclusion
The fact that it is possible to achieve forged mechanical properties on an actual application today is a huge leap in Additive Manufacturing for orthopedics. This exciting development allows us to unlock the potential of additive manufacturing for, yet again, another group of implants. It is now up to the device designers in orthopedic companies, and others, to push the boundaries of AM and realize ideas which were thought impossible. Additive Minds is looking forward to working together with you, unlocking these possibilities, and making the next generation of implants possible.
Author: Davy Orye