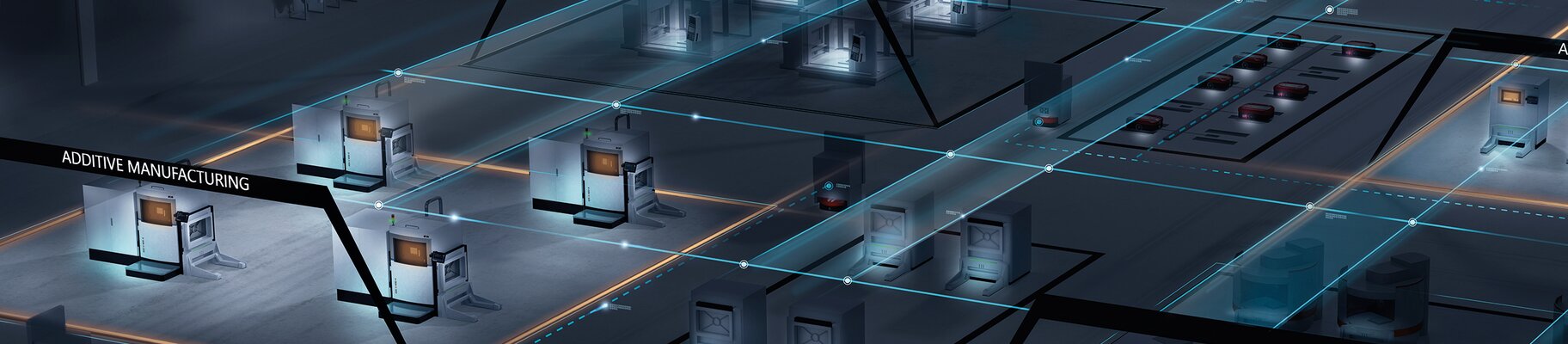
What to consider when thinking about Operational Availability in Additive Manufacturing?
May 12, 2022 | Reading time: 4 min
Operational availability is a formal metric in systems engineering that indicates how long a system was available compared to the time it could have been used based on defined downtime calculations. It has been established in the traditional manufacturing industry for years and is increasingly being discussed in the comparatively young additive manufacturing sector. But how can it be applied in this evolving industry?
Why should I think about operational availability when looking at additive manufacturing?
Additive manufacturing (AM) is an ever-evolving technology used in the shopfloors of a variety of industries, such as aerospace, automotive or turbomachinery. They are all depending on production capability and reliability. With the growing integration of AM into production environments, it is important to consider how the metric of operational availability can be applied here. The EOS white paper "Operational Availability" describes the framework conditions based on the guideline "VDI 3423 Technical availability of machines and plants" of the VDI Verein Deutscher Ingenieure e.V. (Association of German Engineers).
What’s keeping production managers awake at night?
Unplanned machine downtime and outages are not only frustrating, but also have an impact on their business. This is one of the largest causes for loss in productivity, is causing delays resulting in unhappy customers, and lost revenue. Main reasons for unplanned downtime are hardware failures, lack of preventive maintenance or the non-use of original (OEM) parts & consumables. In addition, 50% of the average machine potential is untapped due to inadequate training. That’s why operational availability is not only influenced by the machine itself but also by its service and operation.
How can I calculate operational availability when it comes to additive manufacturing?
Common understanding is key! The guideline VDI 3423 is the standard and emphasizes, what to be agreed and specified between the supplier and the user as part of an operational availability process. There are clear explanations of what is meant and how it is defined. The guideline identifies the assignment of individual incidents and discloses causes and responsibilities. It forms the fundament and creates a work basis for the engaged parties.
And what about OEE?
When talking to customers about operational availability, you also often hear the term "OEE," which refers to the overall effectiveness of the equipment. This is the gold standard for measuring manufacturing productivity. Simply said: It identifies the percentage of manufacturing time that is truly productive. An OEE score of 100% means you are manufacturing 100% Quality (only Good Parts), 100% Performance (as fast as possible), and 100% Availability (no Stop Time). This affects the whole production process whereas operational availability quantifies the contribution of the machine supplier.
- (Operational) Availability: Considering unplanned and planned downtimes
- Performance: Considering slow cycles and small stops
- Quality: Considering defects of produced parts
- Overall Equipment Efficiency: Considering all losses