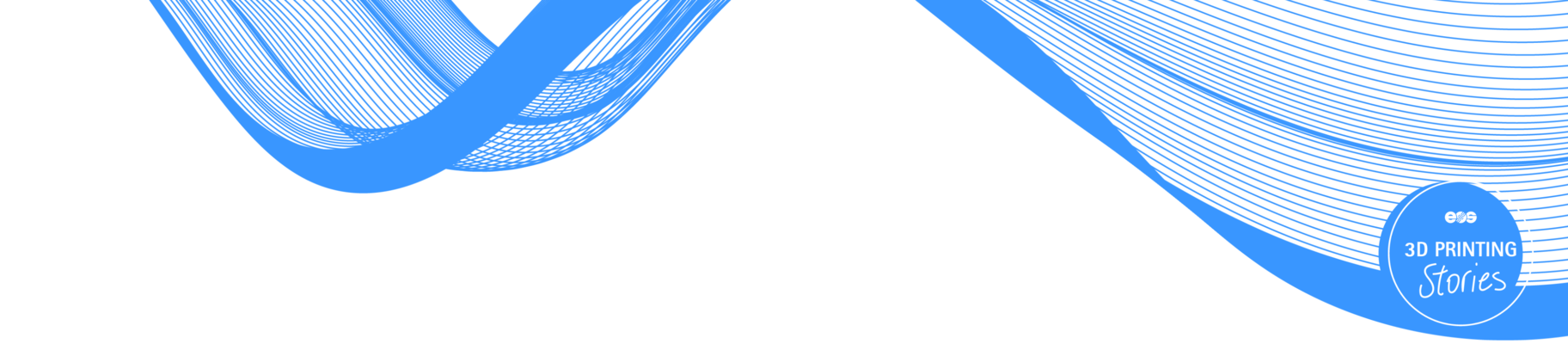
Key to Sustainable Dual-Fuel Hydrogen Technology
CMB.TECH advance sustainable dual-fuel hydrogen technology through 3D printing
JULY 18, 2024 | Reading time: 10 min
How the design freedom of 3D printing is enabling sustainable dual-fuel hydrogen technology
CMB.TECH, designs, builds, owns, and operates large marine and industrial applications that run on hydrogen and ammonia. For over a decade the team have been working on hydrogen-diesel dual-fuel combustion technology. The goal is to decarbonize1 large maritime and industrial applications; that's where 3D printing comes in. Existing diesel engines can be converted into dual-fuel engines2 by injecting hydrogen into the combustion chamber using a 3D-printed injection ring. CMB.TECH developed this component in collaboration with Materialise, a member of the EOS Contract Manufacturing Network for 3D printing. The aluminium part, manufactured using selective laser melting (SLM), meets the material preferences of most engine manufacturers. Not only is the resulting part lightweight at only 654 grams, but the cost of the production was reduced by 25% with metal 3D printing in comparison to traditional casting. For the team at CMB.TECH, the decision to use additive manufacturing (AM) was clear.
1Climate change mitigation (or decarbonisation) is action to limit the greenhouse gases in the atmosphere that cause climate change. Climate change mitigation actions include conserving energy and replacing fossil fuels with clean energy sources. Source: Wikipedia, 18.07.2024
2Dual-fuel engines suck in a gas-air mixture that is ignited by a small amount of injected conventional liquid fuel, which burns (pilot ignition) and then ignites the gaseous fuel-air mixture. Source: Wikipedia, 18.07.2024
Upscaling with metal 3D printing
Roy Campe, CTO of CMB.TECH, explains that the optimal mixing of hydrogen and air is achieved through an internal ring structure, easily and quickly developed through AM. "AM has changed our entire perception of what is possible and improved the overall concept. We couldn't just incorporate these design features into something made by casting or any other traditional manufacturing process." After a successful proof of concept and the first tests with Materialise, the serial production has been started. "Everything from machining to assembly is much easier if you can eliminate the complexity in the design phase by using AM. Materialise takes care of everything and we get a completely finished part," explains Roy Campe.
Understanding the customer's point of view
For Materialise, a crucial initial step in customer engagement is understanding where they stand in their 3D printing journey. This is essential regardless of the industry, as it is the only way to develop a customized program that meets the individual priorities of the customer. Identifying the business and technical drivers that motivate customers and how 3D printing can impact their business models is important. This is not just about cost efficiency, but also about the ability to create innovative designs and complex structures that would not be possible with traditional manufacturing methods. Methods such as opportunity identification, technology and material feasibility assessments, and design and engineering for AM come into play. These approaches help explore and leverage the benefits of additive manufacturing.
According to Materialise, the collaboration with CMB.TECH is a good example of transforming challenges into benefits through 3D printing:
· Time to market
· Management of component complexity with internal hydrogen channels
· Enhanced performance
· Increased functionality enabled by design freedom
Making the difference
For CMB.TECH, 3D printing represents a potential breakthrough in attaining an ambitious goal: carbon neutrality by 2050. Even though there is still a long way to go, CMB.TECH's dual-fuel technology is making a difference. This streamlined system can reduce CO2 emissions from conventional diesel engines by up to 80%, depending on the application and circumstances. "So far, hydrogen injection has been the best method of introducing premixed hydrogen into the air stream,” said Campe. “This allows us to offer CO2 savings immediately. The demand and interest from customers to be able to do this is absolutely massive."

A revolution is coming
The dual-fuel revolution is in full swing, and CMB.TECH is at the forefront. With incoming orders, CMB.TECH can effortlessly produce the required parts, relying on AM and its benefits. Short lead times allow for on-demand ordering, which reduces risk and storage costs. They also allow for on-demand ordering, reducing risk and inventory costs. As with many AM projects, CMB.TECH's next steps will focus on continuous development – optimizing design, expanding the project to various applications, and minimizing material and costs wherever possible.
Materialise also looks positively to the future: the collaboration since 2019 has been a partnership that has developed and grown steadily, with increasing integration between the two teams. Materialise’s AM expertise and capabilities complement CMB.TECH's drive for innovation and desire for change at every step. Collaborating with customers requires a deep understanding of their individual needs and challenges. Through targeted analyses, tailored programs, and leveraging the unique benefits of AM, these challenges can be successfully addressed. EOS technology plays a crucial role in this process. The introduction of AM is significantly advanced through the collaboration between EOS and Materialise along the AM value chain. With EOS's modern AM machines, Materialise benefits from a high-quality standard production process, which significantly enhances the quality and efficiency of its manufacturing. With the experience and advantages gained from using EOS technology, the Contract Manufacturing Network Partner is well-equipped to meet the diverse requirements of its customers and play a decisive role in shaping the future of manufacturing. The collaboration is characterized by trust and integration, and all parties share the common goal of making the world a better and healthier place.
#3dprintingstories