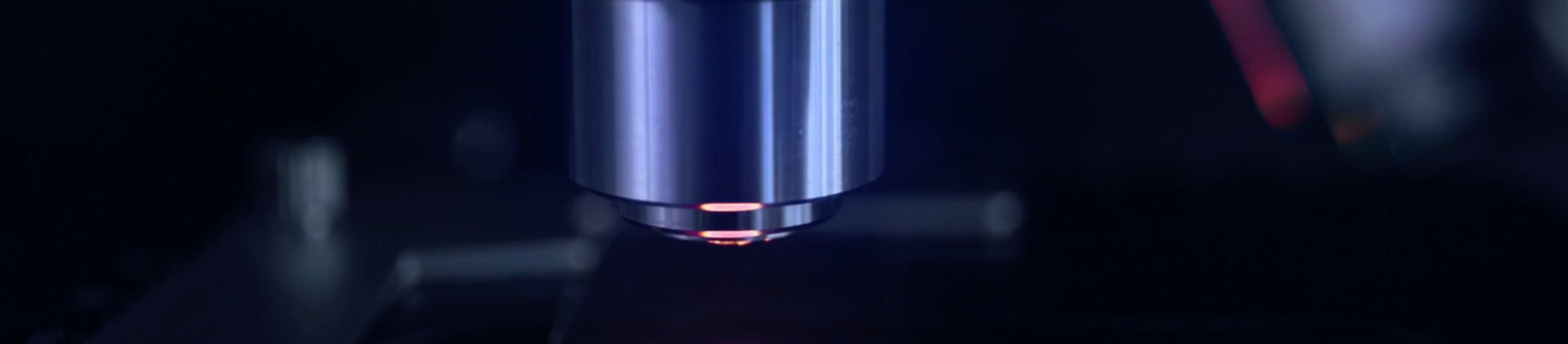
In-Process Monitoring Systems for Metal Additive Manufacturing
September 28, 2021 | Reading time: 4 min
Taking the leap into the additive manufacturing industry can feel daunting. Whether you’ve previously used it in research and development, or are only just getting to grips with the tech - it can get a bit overwhelming with all the options and additions that you need to consider. Add to this quality control and standardized industry testing that’s built off traditional production methods, and it’s no wonder that quality assurance can pose a bit of a conundrum for many manufacturers.
Why is quality assurance such a concern when it comes to additive manufactured parts?
Additive manufacturing isn’t a new process. However, it’s the move from its use in prototyping into a viable production method has meant that traditional methods of quality assurance that are designed around legacy manufacturing methods are not necessarily going to be suitable for testing additive manufactured parts.
In precision-specific industries where the standard of quality for every part requires rigorous testing, there is a challenge as to how a new production technique like additive manufacturing can be safely assessed when no current industry standards exist. This can lead to questions like:
- If there is no standardized testing, how can I be sure that each part I produce is as safe as the traditional parts?
- Additive manufacturing is always evolving. How can quality assurance practices keep up?
- I want to print a one-off part. How can I apply standardized testing without incurring the cost of multiple parts that will be destroyed in testing?
Why should I consider in-process monitoring?
In-process monitoring is the solution to many of the questions surrounding quality assurance and testing ability with additive manufacturing. The ability to not only track your print but collect data on it layer by layer means that you’ve already got an extensive report on your part before it’s left the print bed. With a large range of in-monitoring systems available both as standard with your printer, or from third parties, there is a lot of information to consider. In this white paper, Lukas Fuchs and Christopher Eisher break down the technological principles behind the different options and the practical applications of each.
In Summary...
- The role of additive manufactured parts in many industries is still new and, as such, the rigorous testing practices that were used for old and traditional production methods can’t keep up with the speed of innovation we’re seeing in the additive manufacturing industry.
- Introducing in-process monitoring into your production methods can not only provide insightful data into the efficacy of your part but can also speed up quality assurance while cutting costs.
- There can be challenges to quality assurance when creating additive manufactured parts, but by incorporating the right in-process monitoring system into your build you can avoid these roadblocks.
- Now is a promising time to take the leap into additive manufacturing. With constantly evolving innovation and tools to help you with the quality assurance there isn’t a better time to make that switch.
Want to learn more about in-process monitoring and how it can help with your quality assurance requirements?
Download the full Whitepaper.