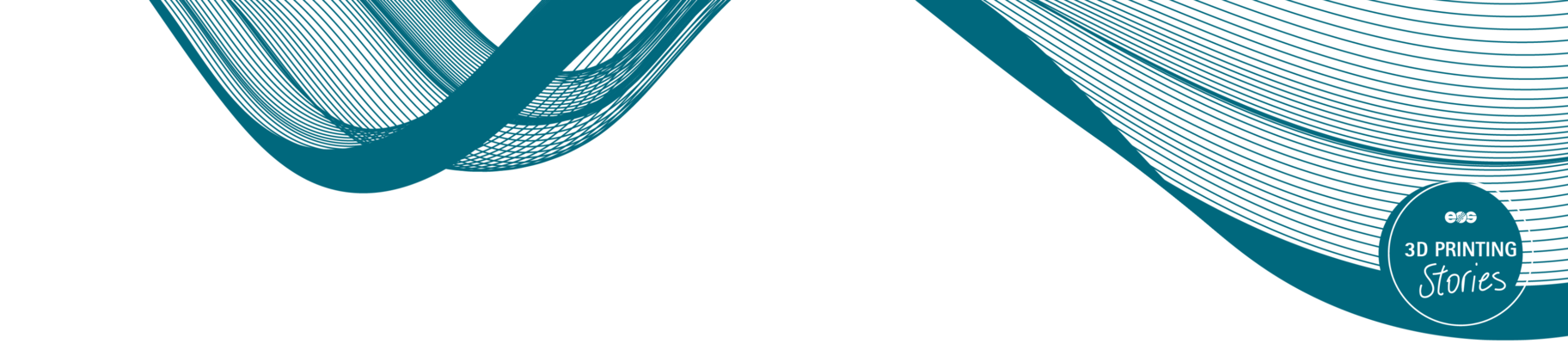
When the journey into the unknown begins once again
Dunlee and EOS unlock the potential of 3D tungsten structures
September 2, 2024 | Reading time: 10 min
2007 was the beginning of the collaboration between Dunlee and EOS on the topic of tungsten. It was triggered by the search for a way to improve the quality of CT images. The result was tungsten anti-scatter grids - a real breakthrough at the time, which shaped the market for several years. Since then, the production process has been perfected and now produces more than 100,000 grids per year. What happens next and why tungsten will play a role in luxury watches, particle accelerators and space.
Back to the roots: The path to the anti-scatter grid
Due to its high density, tungsten is an ideal material for absorbing unwanted scattered radiation. Dunlee wanted to take advantage of this property to become a pioneer in tungsten anti-scatter gratings and significantly improve the image quality of CT images. Jan Philippe Grage, Business Manager 3D Printing at Dunlee, explains the first steps: "My colleagues at the time quickly agreed that a fine structure made of tungsten could only be realized via 3D printing - but this was still in its infancy in 2007. At EOS, however, there was a willingness to go into the unknown.
Until then, walls as thin as 100 μm had not been produced using 3D technology. The first milestone was reached when EOS demonstrated that such fine structures could be realized with steel. In parallel to the technical feasibility work, Dunlee was convinced to invest in the innovative concept. It had to be clarified how the technology could be integrated into the existing factory processes of a large medical technology group. "Once the business case was approved, another important step was taken," says Grage.
A few days after the decision was made, EOS delivered an EOS M 270 3D printing system customized for the application, and work began on the process chain. Proof of concept was achieved in 2012, and the first customer was on board in 2014. "Once it was clear what we had achieved - up to four times higher image quality - the customer was immediately on board. It was a breakthrough that has had a huge impact on the market for several years." In the meantime, EOS M 290 systems are being used, which have been tailored to the customer's needs by EOS' subsidiary AMCM.
More efficient, faster, better: Only the perfect process counts
Like everywhere else, competitors in this product segment did not go into a deep sleep. Players in Europe, China and the United States began to launch similar products, and competition became fiercer. "On the one hand, we specialize in medical technology and therefore know our customers much better than general service providers. On the other hand, we have been working intensively on all our processes in recent years to become more and more efficient," says Grage, explaining Dunlee's market strategy.
The entire process was considered, from incoming inspection to the 3D printing process itself, to handling and measurement of the finished product. A high degree of automation helped to further increase efficiency. Production now runs 24/7 in five shifts, with an annual output of over 100,000 grids. The building process itself is now highly efficient with an 80µm process and tolerances have been reduced to +/-15µm. By 2027, the volume is expected to increase to one million grids per year - produced with EOS and AMCM 3D printing technology.
"We have doubled our capacity with EOS twice in recent years, so there has been a lot of learning on both sides," explains Grage. "I think it's positive that we challenge each other and come up with innovations. An EOS service engineer is on site for five days, and if we need anything else, EOS comes to us. That's great.”

Where do you want to go? Conquering new markets with tungsten
Through process refinements and extensive data analysis in the production of anti-scatter gratings, Dunlee has developed a great deal of expertise in the processing of tungsten over the years. The question now is how this process knowledge can be used for another journey into the unknown. Even though Dunlee's focus is on medical technology, the technology and knowledge can be used for applications in many other industries. These different markets can only be considered if the core process developed together with EOS is suitable. Workflow, component handling and processing vary, but many requirements are already covered by Dunlee's ISO certification ISO13485.
"We are currently looking at applications in non-destructive testing, for example. Here, too, CT systems must deliver high image quality, whether in the security scanner at the airport or in product scanning. Another area of interest, according to Jan Philippe Grage, is nuclear fusion, which is the subject of intensive research worldwide. With its high melting point (3,422 °C) and very high material density, tungsten has two properties that are required for components such as deflection plates, cooling channels or other fine structures in the infrastructure of particle accelerators. And then Dunlee is looking at a completely different segment, namely luxury watches. Why is that? Grage explains: "Tungsten has a high density and is therefore suitable for very small components that need to be heavy. As a result, a tungsten counterweight can be used very well in the small space of a watch.
All in all, there are many reasons for EOS and Dunlee to continue working closely together on 3D tungsten structures. Grage concludes: "We really appreciate the cooperation and hope that together we can address the requirements behind the production of even more stable tungsten structures. This means that the journey can continue.”
#3dprintingstories